Volkemon
New member
2006 VTX 1800 Motortrike rearend R&R - Fix Broken Welds for Ladder Bar Mount -
Hi There! :wave4:
This is a sub-topic thread about my adventures with a 2006 Honda VTX 1800 Motortrike conversion. Got a good deal on it, and am paying for that now.
Main thread here - https://www.triketalk.com/forum/threads/55731-2006-Motortrike-vtx1800-might-be-my-next-ride
Last ride, hitting 3rd gear, the bike started to crab right. I let off, kept my cool and went home carefully.
Jacked it up, and found the axle moved fore and aft on the right side. Removed the upper cover to see this -
The bottom crack is FRESH.
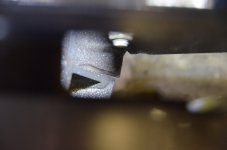
So time to pull the rear axle.
****************************************************************
Removed the body.
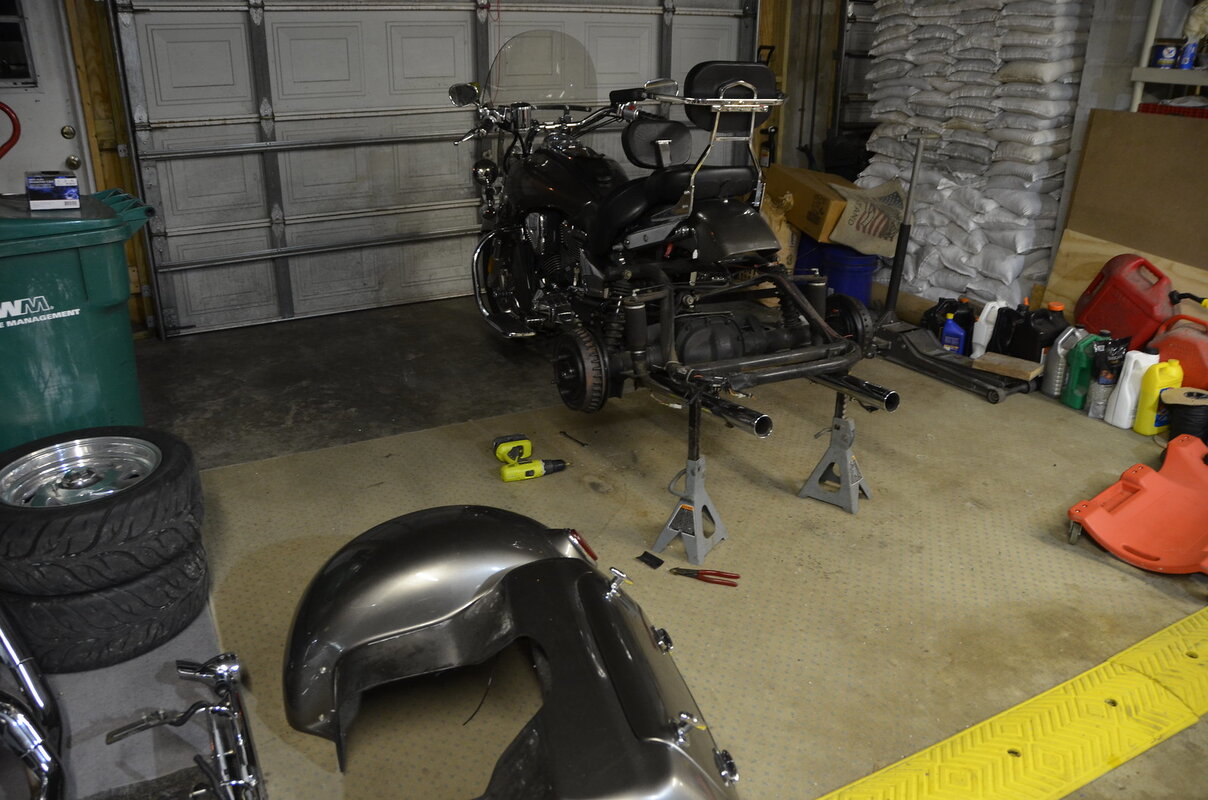
**************************************************************
Rear axle on the jack.
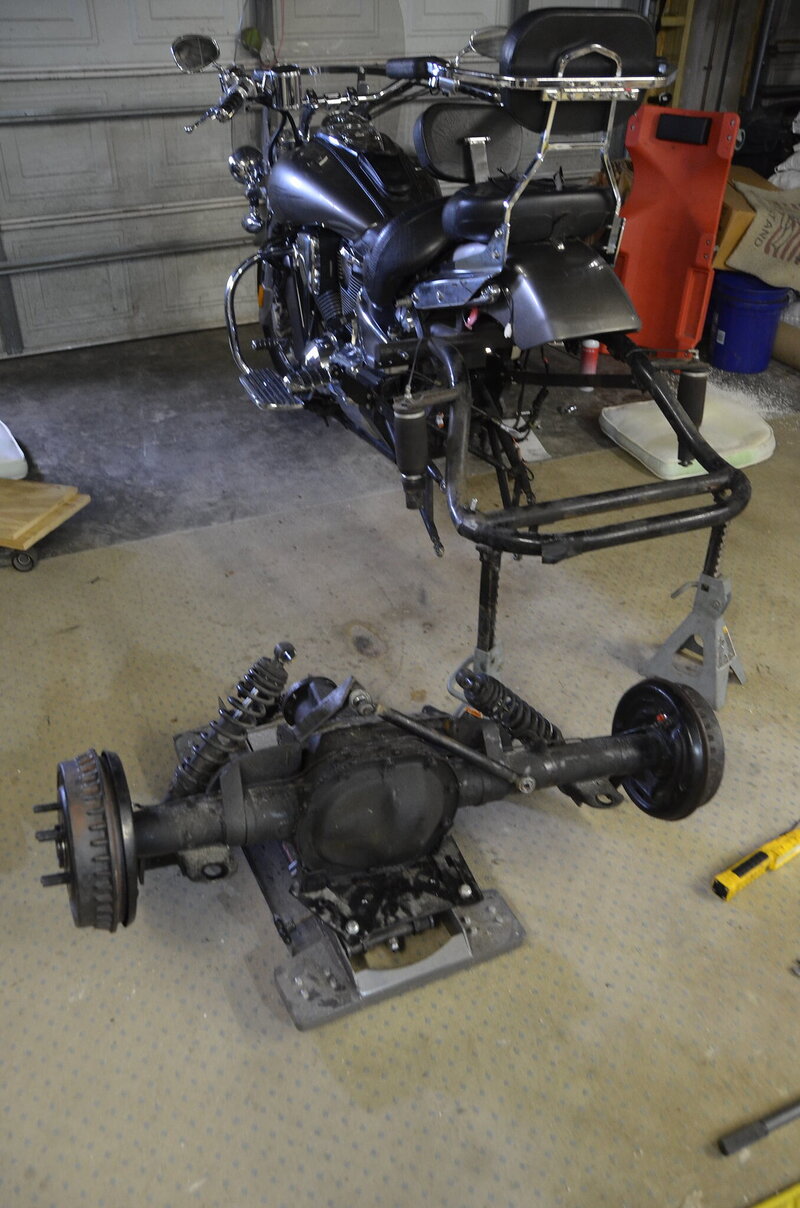
*************************************************************
Couple issues..
Someone installed LED lighting, the 4blk1r ribbon cable. Pushed through from the other side. When doing so, they got the wire harness pushed closer to the rear cylinder exhaust. Will inspect carefully, re-locate, and maybe make a small heat shield. Looks OK on first glance.

and wanted to remove the ladder bars, but hit a stopper.
This is the cover that was glued on, the pivot 'fasteners' are behind it.
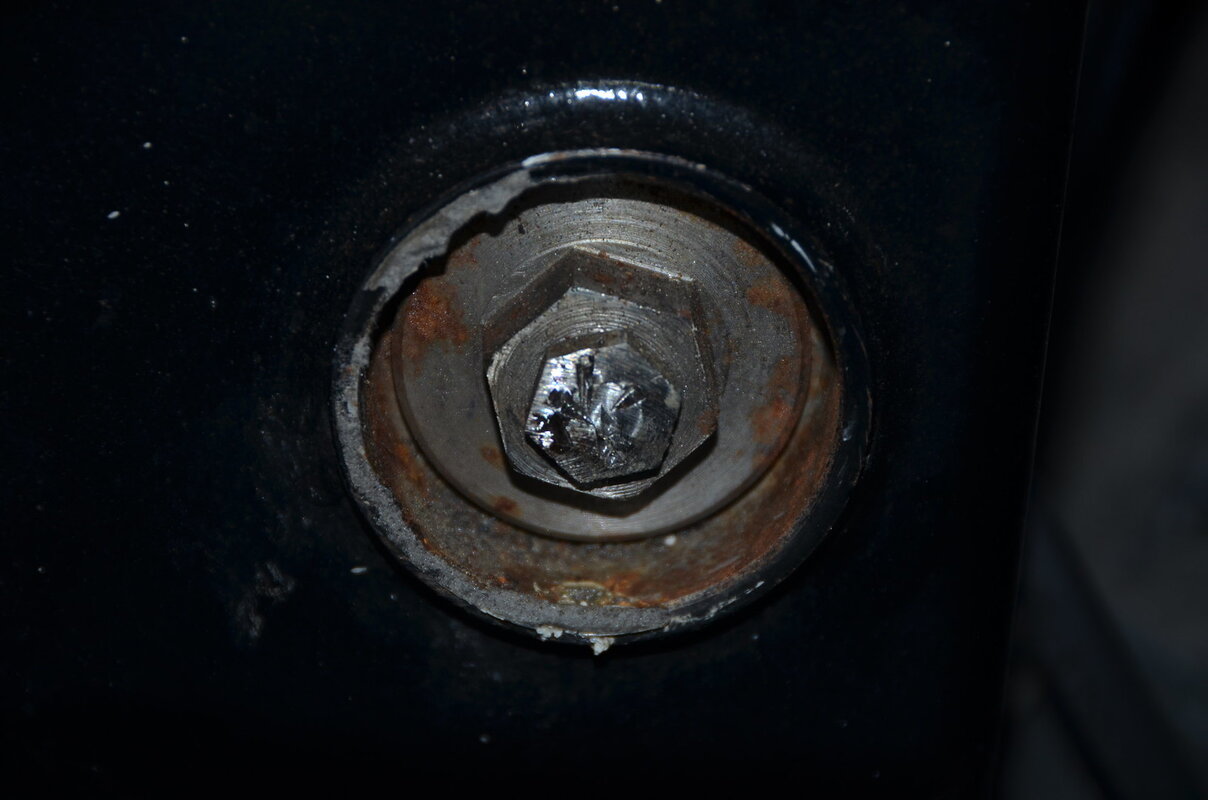
Looks like there is a nut ground flush, and locked with a chisel.
*********************************************************
This is the other side showing the ladder bar end. Is that a carriage bolt end?!? -
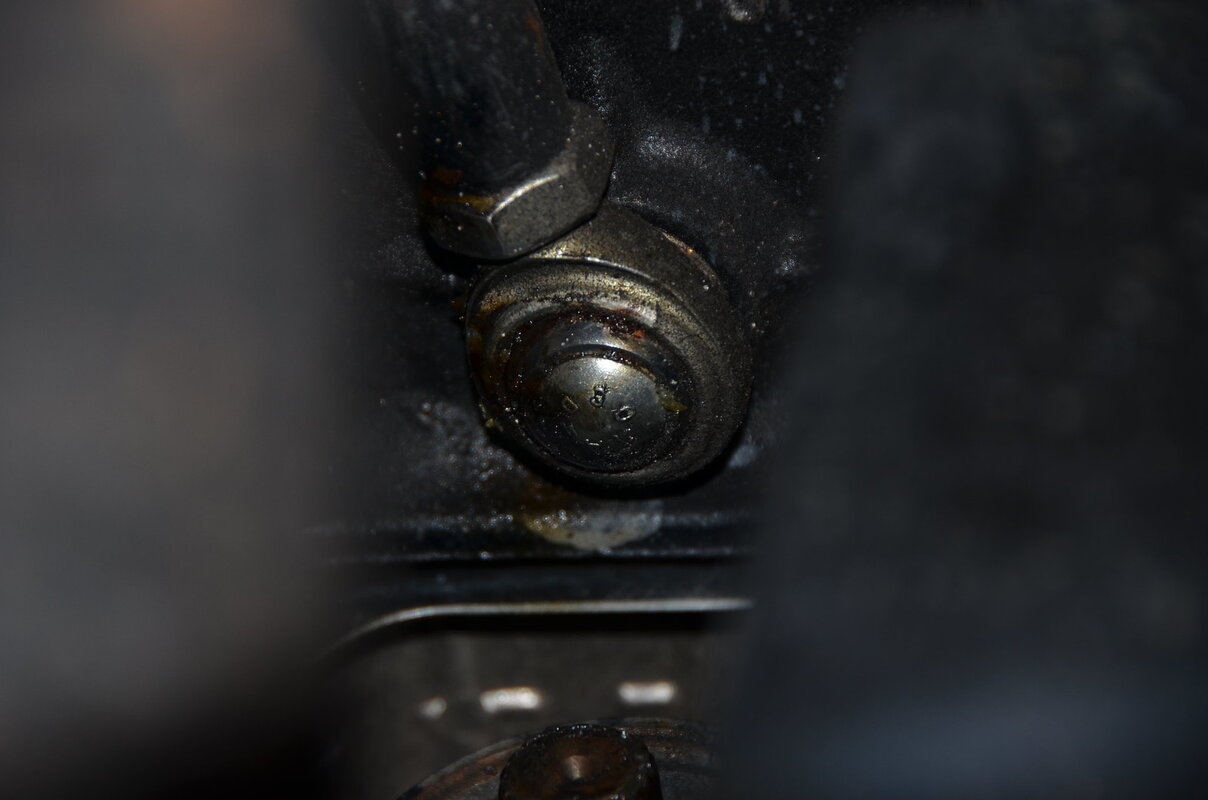
So... I am SO hoping that the carriage bolt is just stopping the side to side movement, and there is a separate sleeve that threads on from the other side that the bar pivots on.
I am REALLY hoping the main pivot point for the ladder bars is NOT soft carriage bolts...
So I can maybe grind off the small nut, and slide the remains of the bolt out? Then unscrew a pivot and allow the drag link to be removed...
And on the left side. I have no idea how this comes off, might be glued like the other side. Little help?
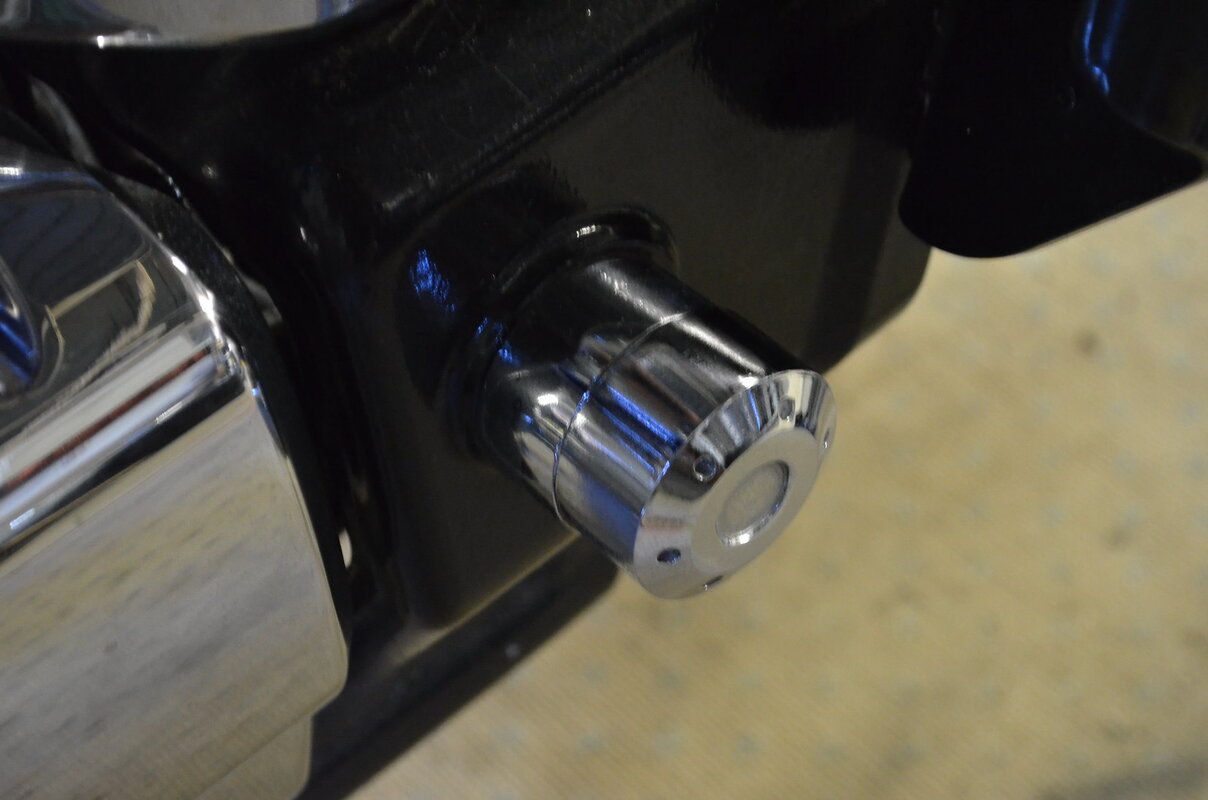
OK, on to part 2... dissecting the remains and assigning blame.
Hi There! :wave4:
This is a sub-topic thread about my adventures with a 2006 Honda VTX 1800 Motortrike conversion. Got a good deal on it, and am paying for that now.
Main thread here - https://www.triketalk.com/forum/threads/55731-2006-Motortrike-vtx1800-might-be-my-next-ride
Last ride, hitting 3rd gear, the bike started to crab right. I let off, kept my cool and went home carefully.
Jacked it up, and found the axle moved fore and aft on the right side. Removed the upper cover to see this -
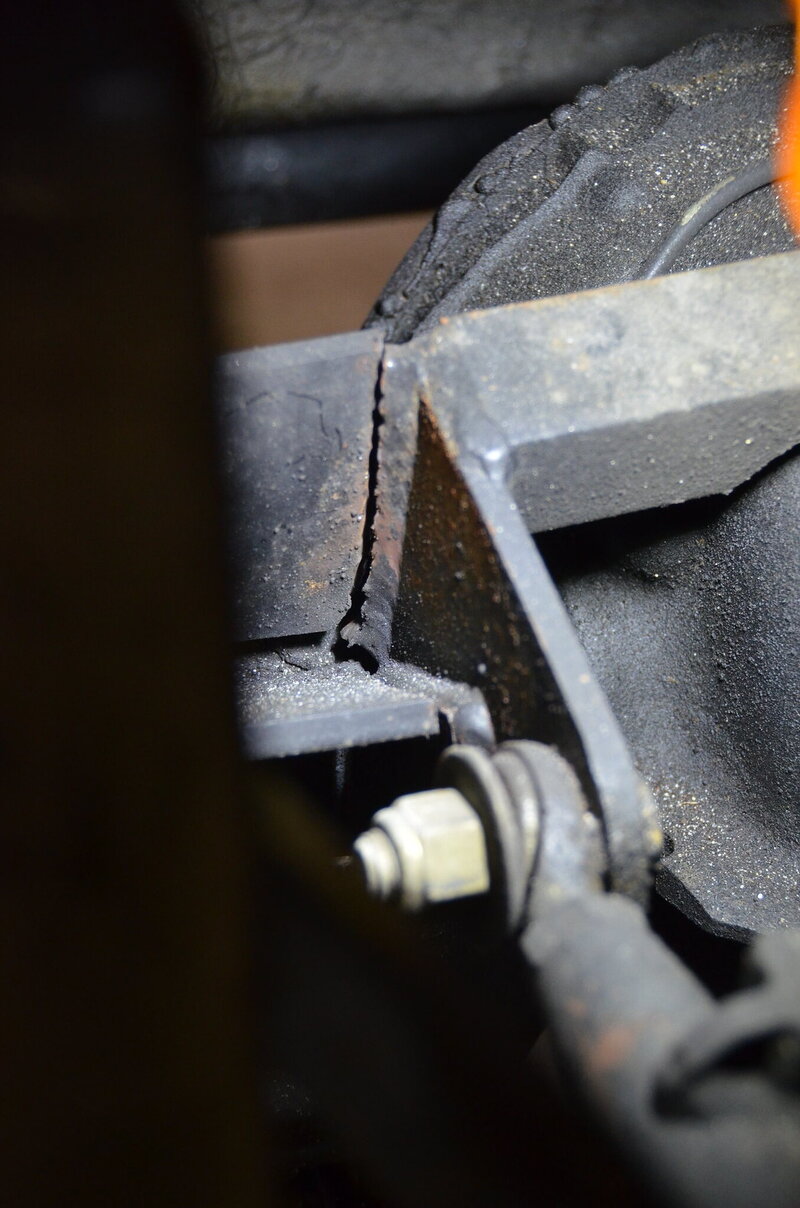
The bottom crack is FRESH.
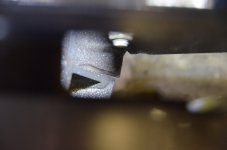
So time to pull the rear axle.
****************************************************************
Removed the body.
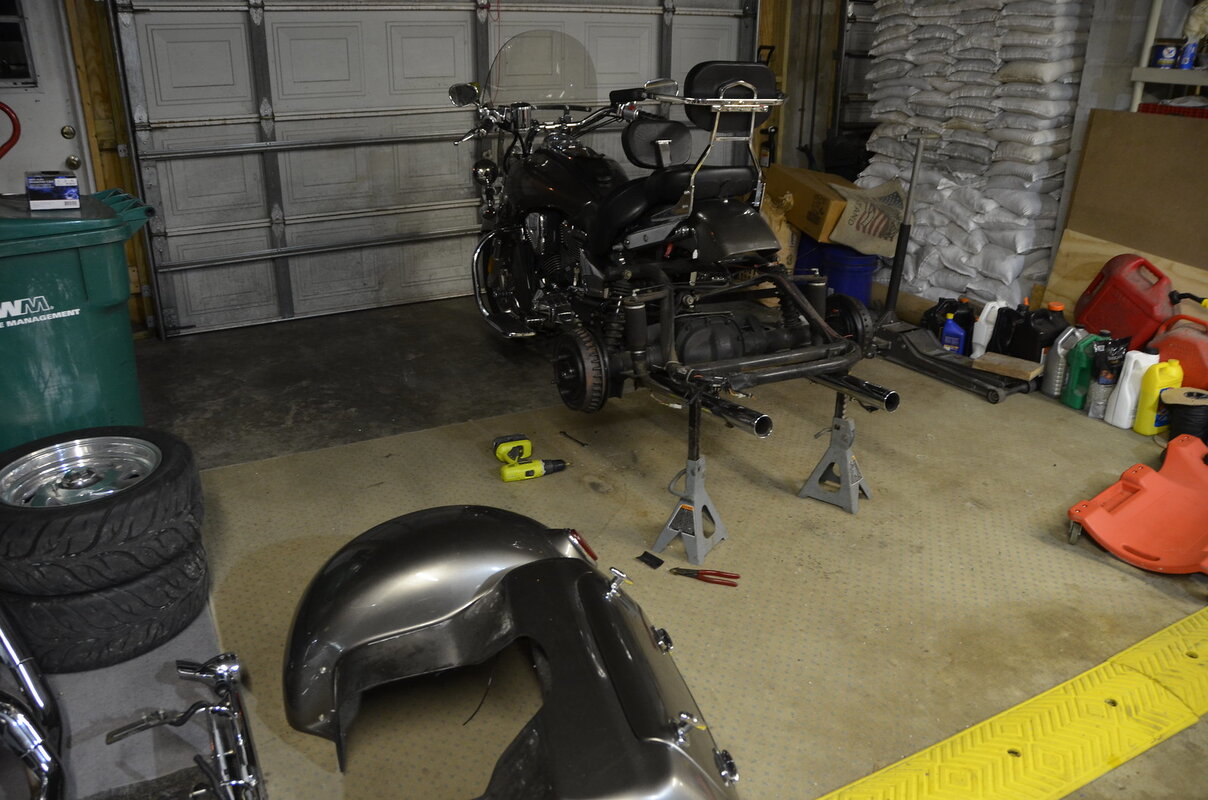
**************************************************************
Rear axle on the jack.
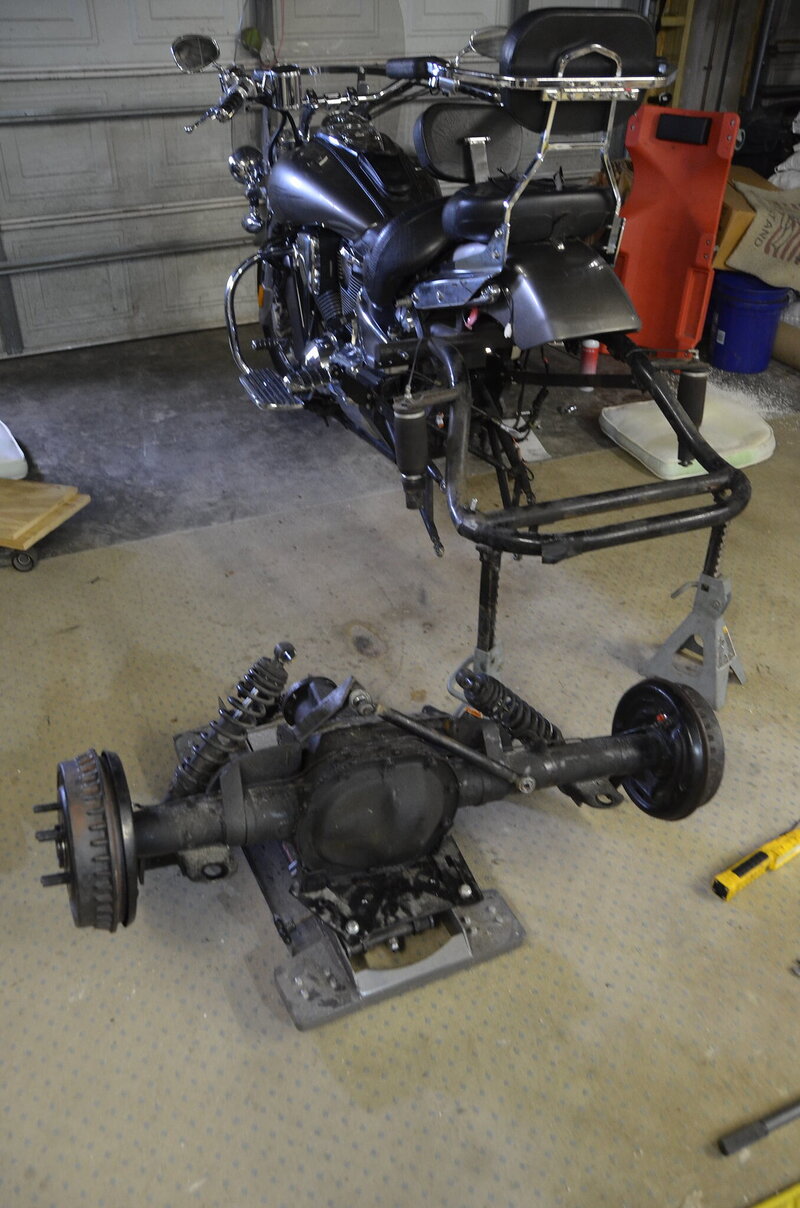
*************************************************************
Couple issues..
Someone installed LED lighting, the 4blk1r ribbon cable. Pushed through from the other side. When doing so, they got the wire harness pushed closer to the rear cylinder exhaust. Will inspect carefully, re-locate, and maybe make a small heat shield. Looks OK on first glance.

and wanted to remove the ladder bars, but hit a stopper.
This is the cover that was glued on, the pivot 'fasteners' are behind it.
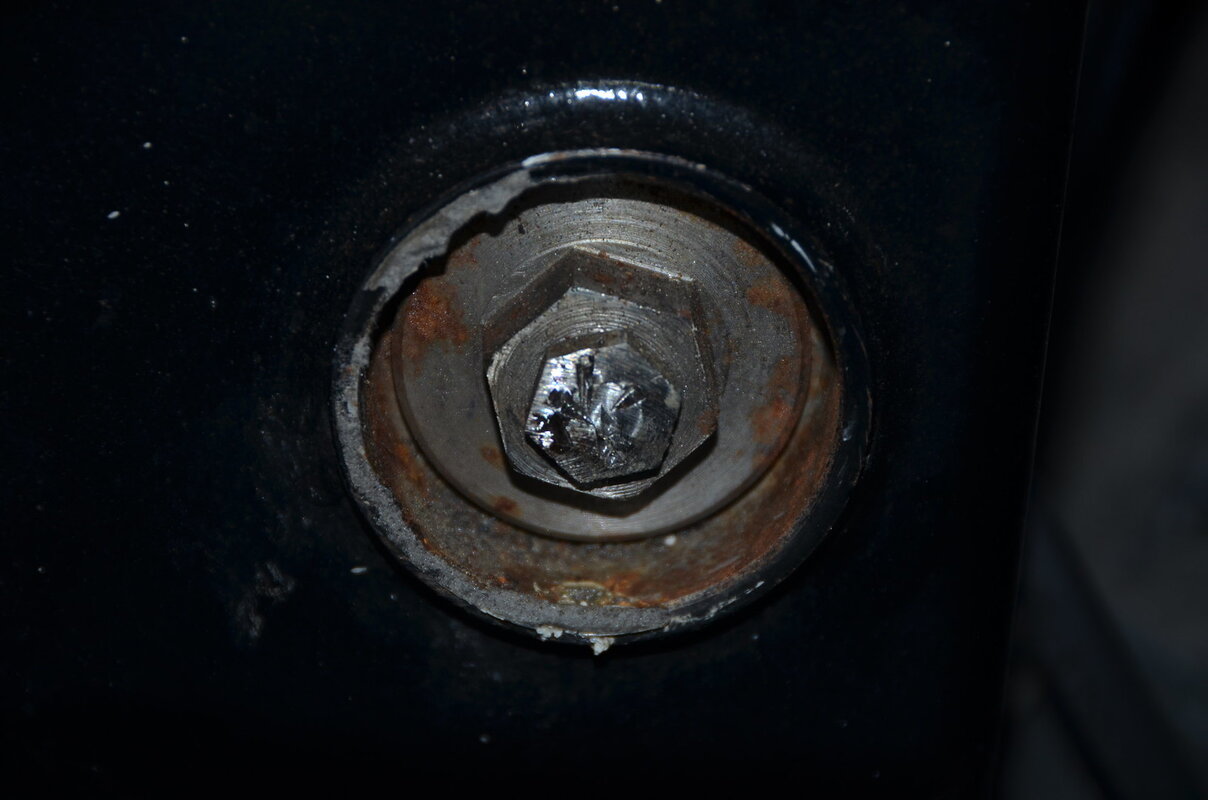
Looks like there is a nut ground flush, and locked with a chisel.
*********************************************************
This is the other side showing the ladder bar end. Is that a carriage bolt end?!? -
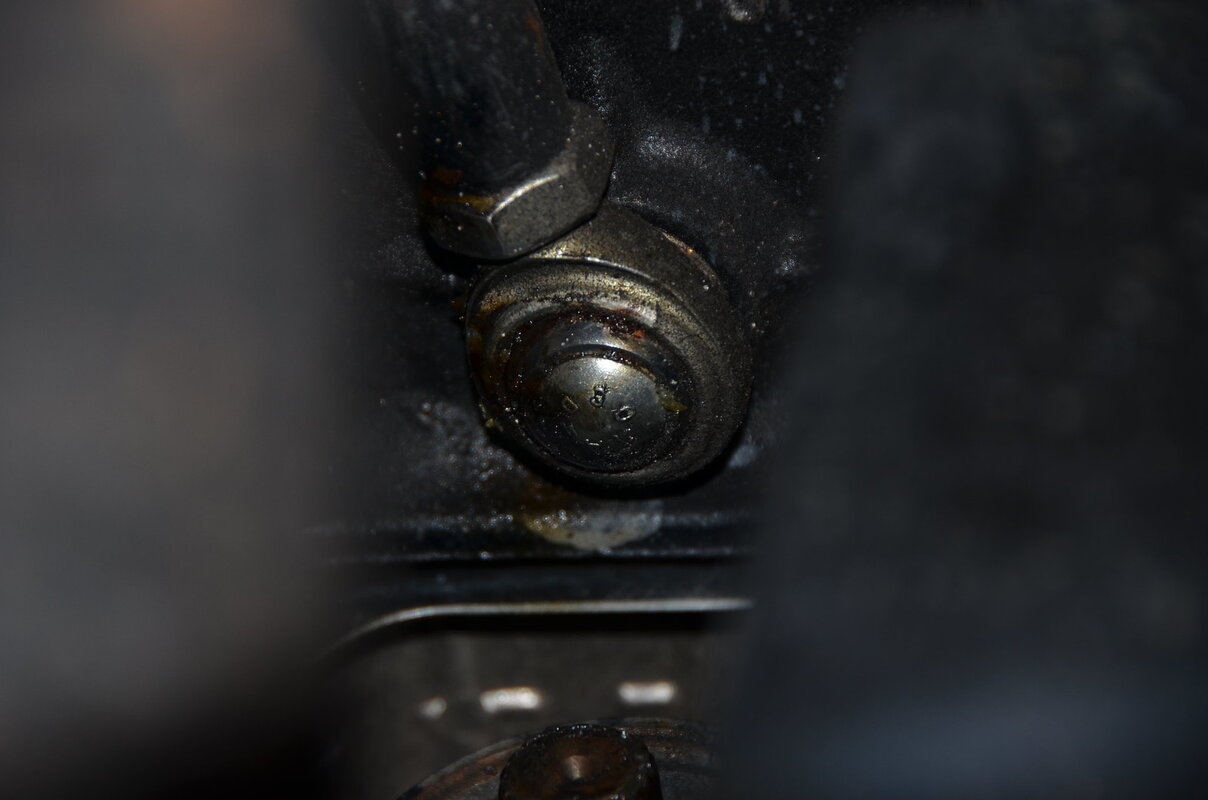
So... I am SO hoping that the carriage bolt is just stopping the side to side movement, and there is a separate sleeve that threads on from the other side that the bar pivots on.
I am REALLY hoping the main pivot point for the ladder bars is NOT soft carriage bolts...
So I can maybe grind off the small nut, and slide the remains of the bolt out? Then unscrew a pivot and allow the drag link to be removed...
And on the left side. I have no idea how this comes off, might be glued like the other side. Little help?
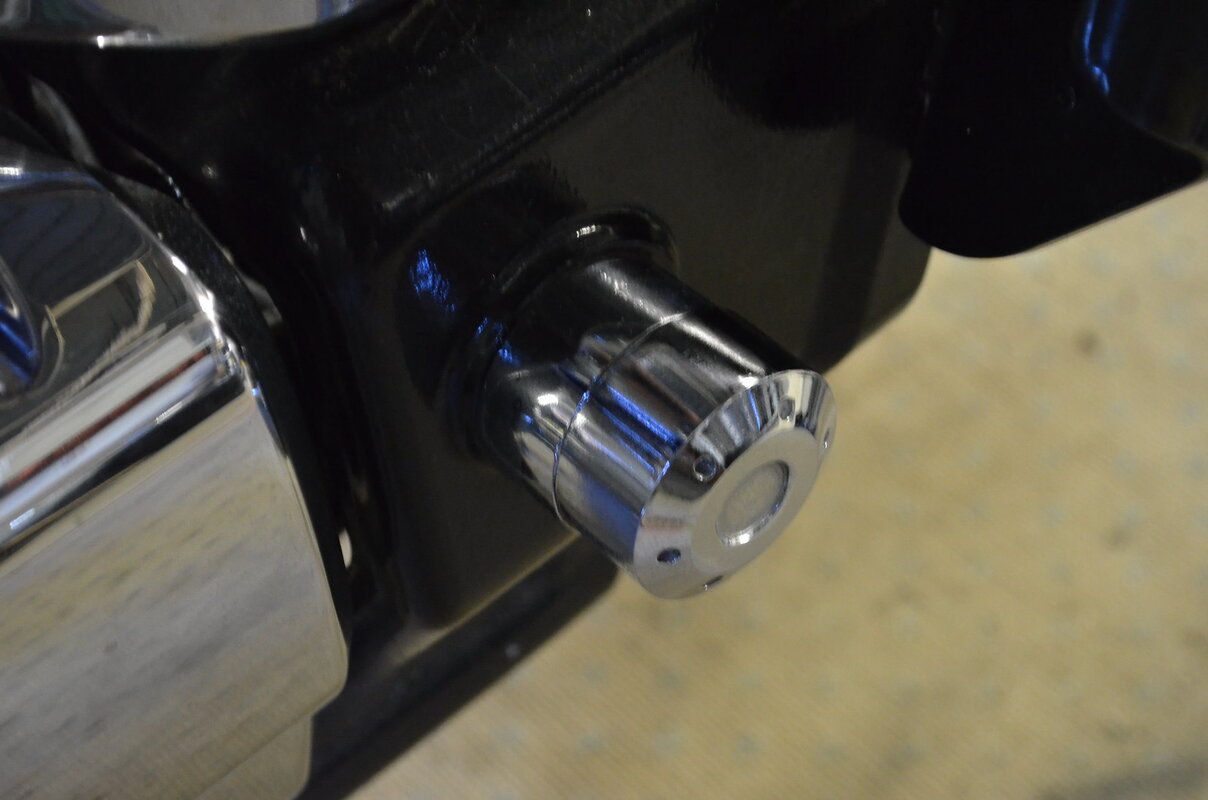
OK, on to part 2... dissecting the remains and assigning blame.